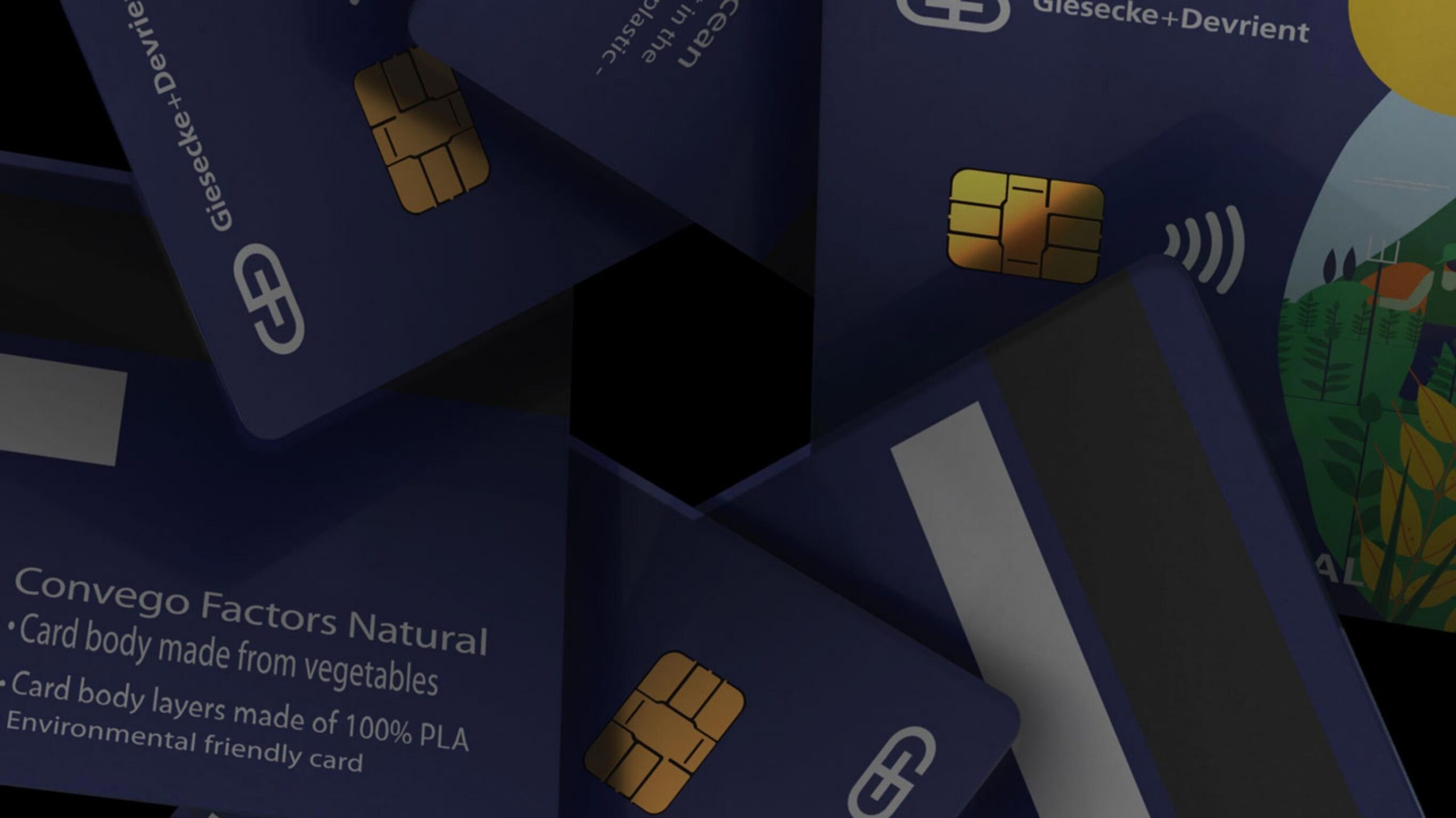
The
Card
Journey
Let’s go!
It can be an extremely complex process to manufacture a payment card and implement all of its security and connectivity features. Through this virtual tour, we want to give you an idea of the vast range of possibilities we can offer you in a dynamic and relaxed way.
We will detail the entire manufacturing process in three main stages, from preparation of the printing materials to addition of the security features. We hope this tour gives you a detailed idea of what we can do.
STAGE 1 PREPRESS
Planning the journey
They say the only rule of travel is not returning the same as you were when you left. This will definitely be the case for our travelling friend, the card. Starting as a simple idea or project in our customer’s mind, it will have become a completely different thing by the time it finishes its journey.
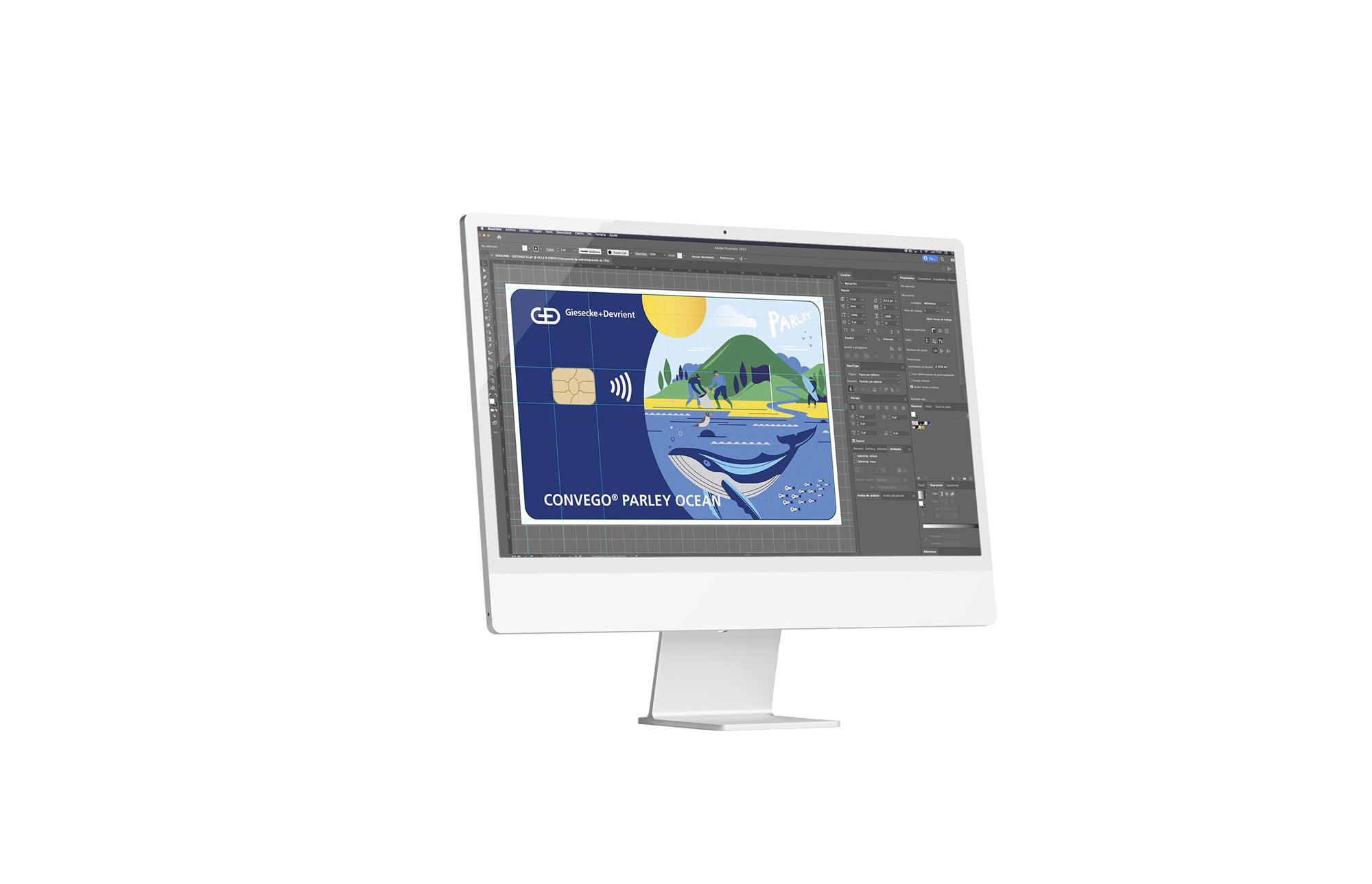
Choosing the perfect combination of flights
Our card's journey begins with the customer's order. Our graphic design team then prepares the future card’s design. It is usually the customer who sends a preliminary design. Our designers then adapt it to comply with Visa, Mastercard or other applicable regulations, as well as to ensure the design’s production feasibility in our manufacturing equipment. They also enrich it to make it more appealing.
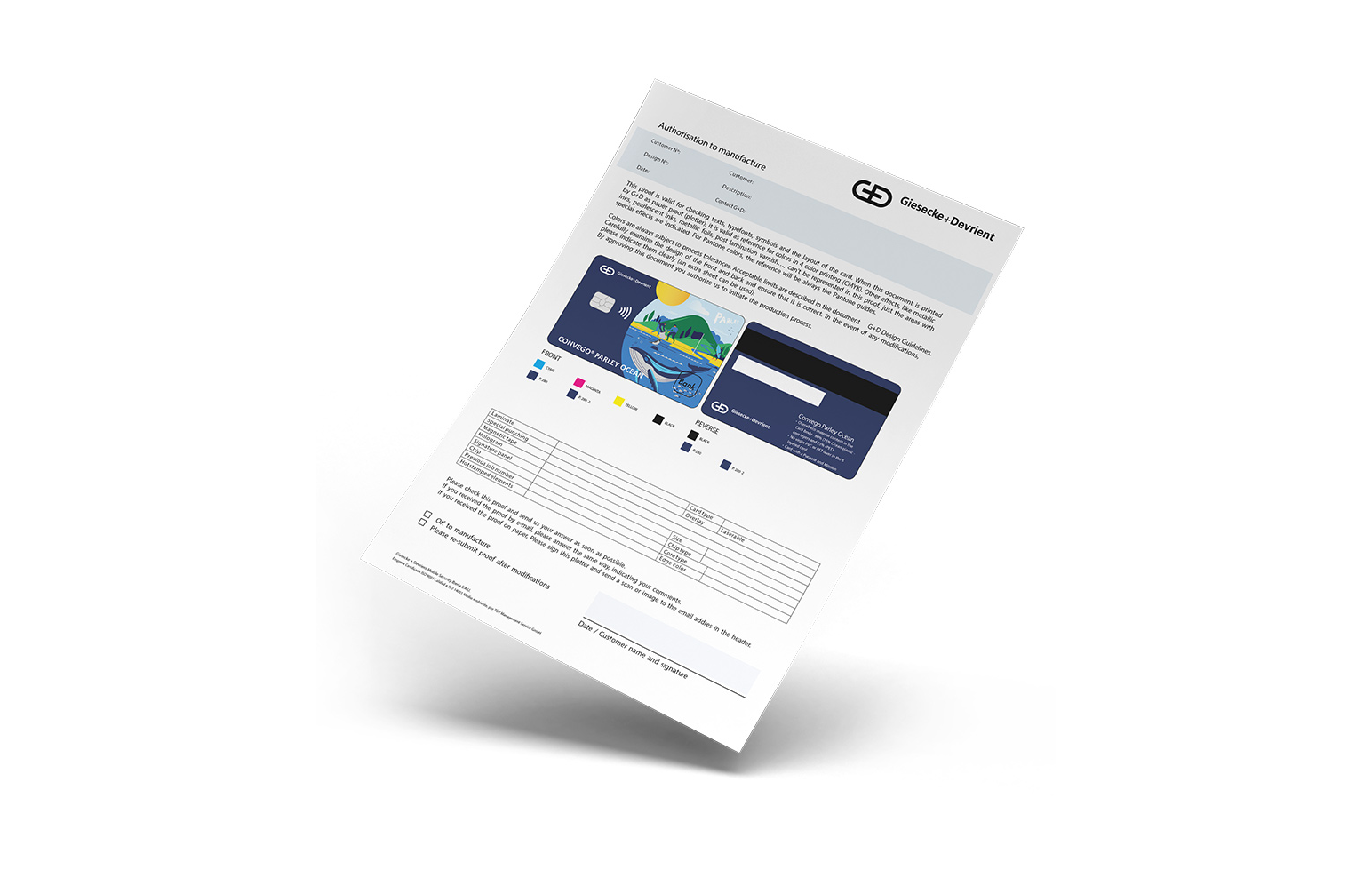
Don't forget the Check-in
Once we have adapted and prepared the design, an electronic sample is created. The electronic sample is a document containing the design of the card (front and back) and all of its important details (colours, location of the different elements, finishes, type of chip and magnetic stripe, type of core or substrate to be used, etc.).
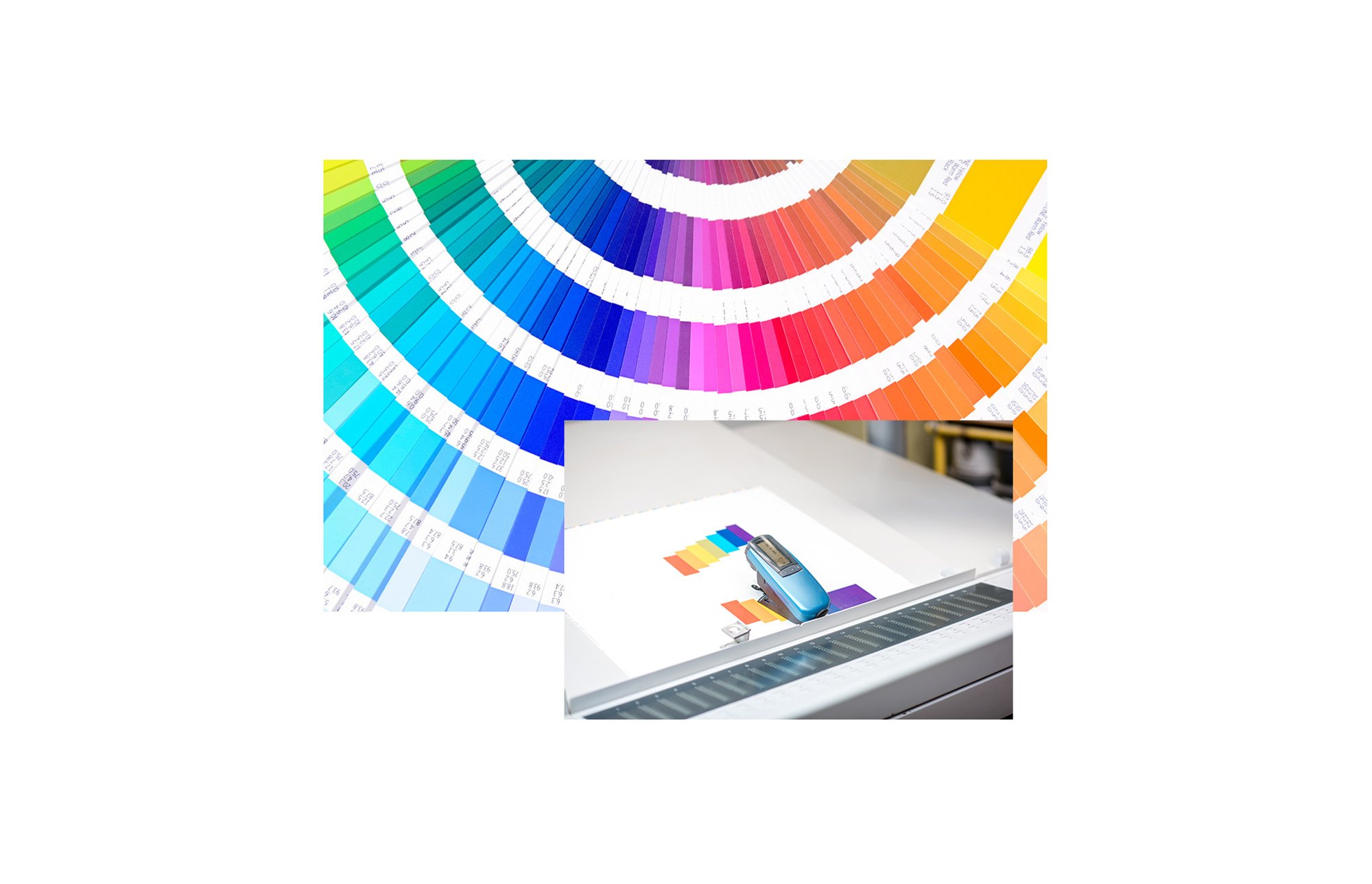
Since, in most cases, the bank card is the only physical item from the bank that users will hold in their hands, it is very important to respect the colours, logos and other elements of the customer’s corporate image on the card to the greatest possible extent.
The electronic sample is sent to the customer and the payment scheme (Visa, Mastercard, etc.) for review and approval.
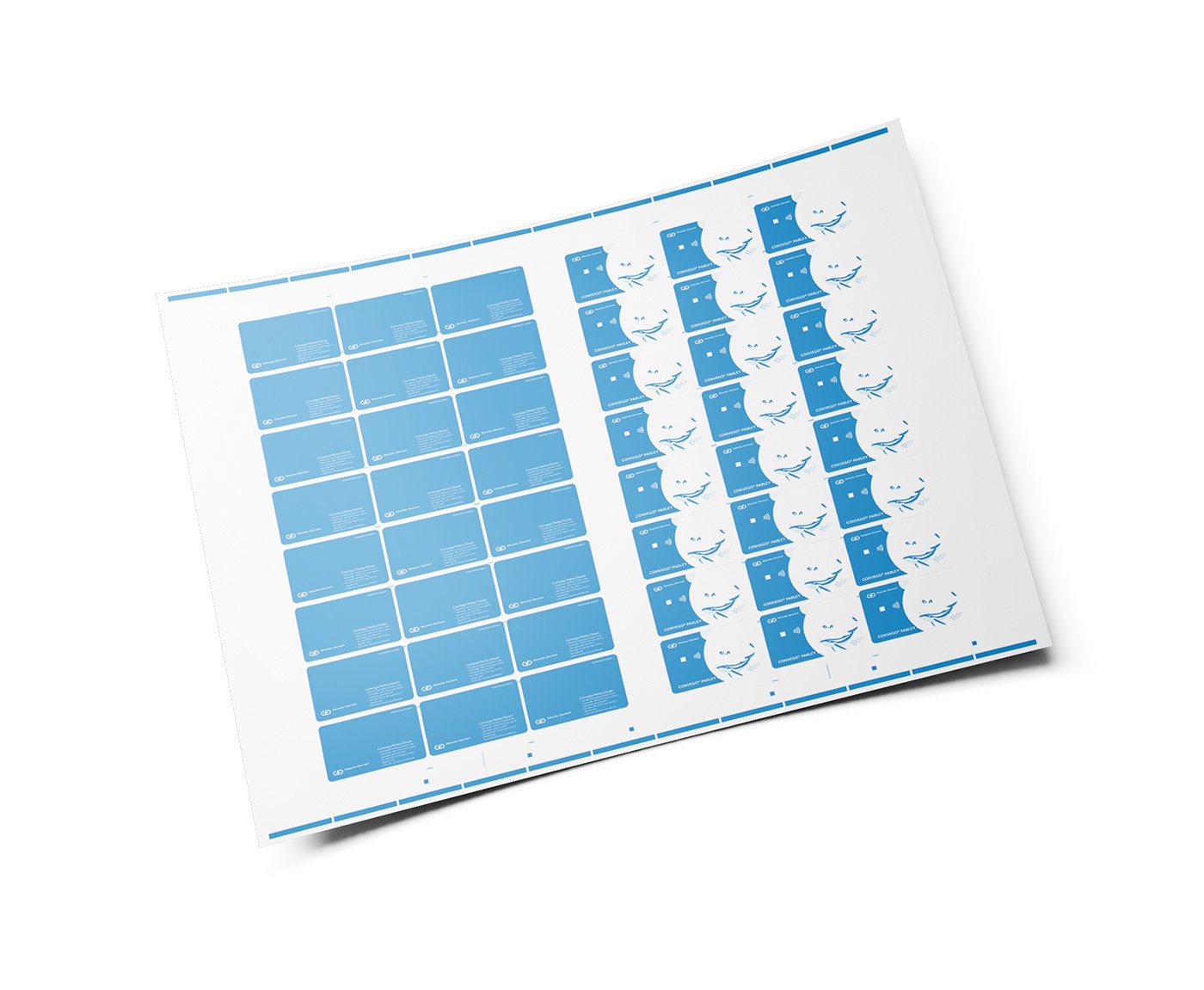
Window or aisle seat?
Once the electronic sample has been approved we use CTP (Computer to Plate) or CTS (Computer to Screen) pre-press equipment to prepare the offset plates or screen printing screens that we will use to print the designs.
Video: Prepress Stage
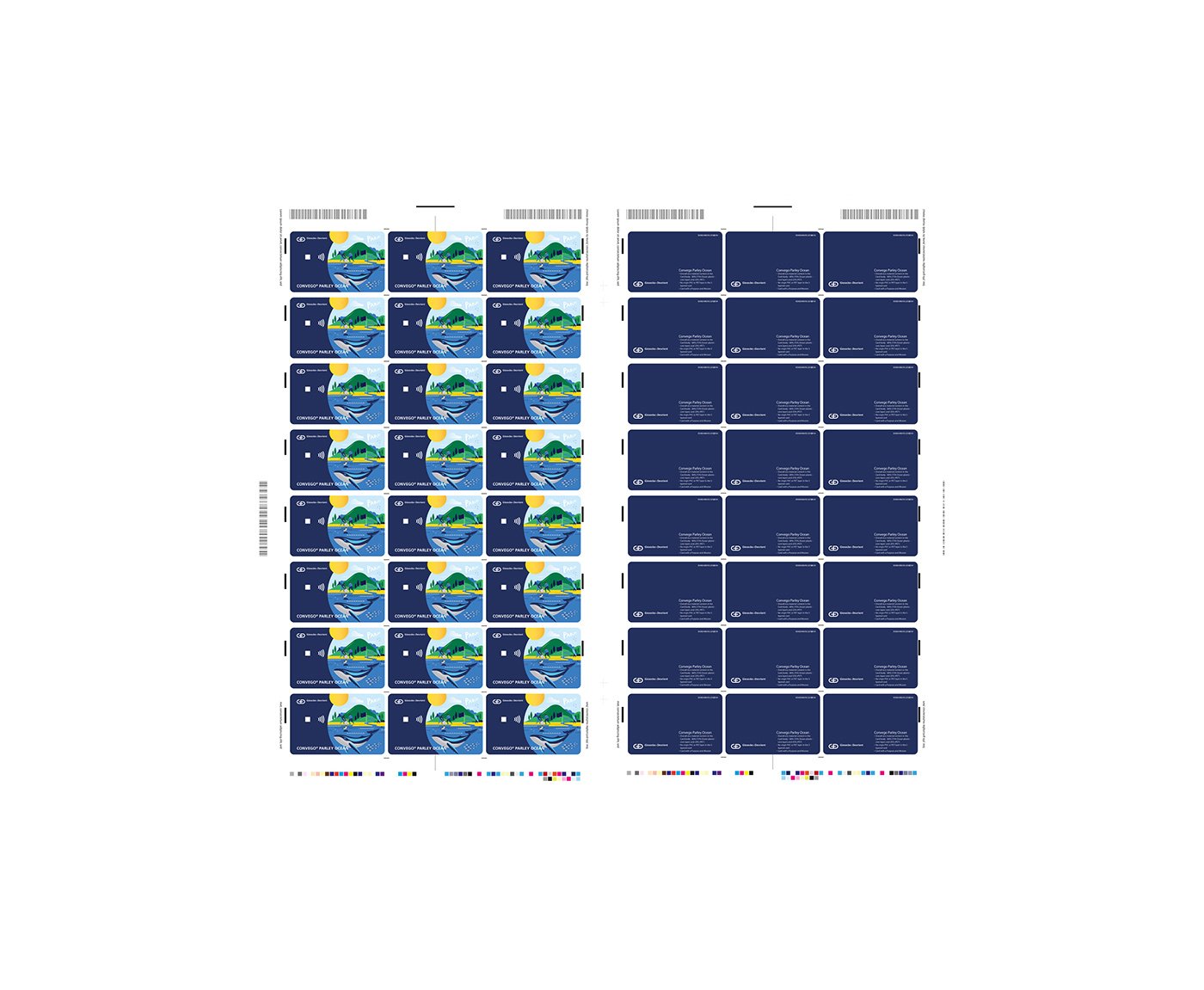
STAGE 2 PRINTING
Get ready for take-off
Now enough speed has been built up, it is time to taxi to the runway and start the card printing process. The offset plates and screen printing screens created in the previous stage will be used to print the front and back of the card.
The plates are fitted in the printing machine, the inks are adjusted and the substrate to be used to print the cards is placed in the feeder.
Coffee or tea?
PVC, r-PVC, PLA, r-PET are not crew nicknames. They are the main substrates we use to manufacture our cards.
Our airline, which increasingly cares for the environment and our travellers’ current needs, is firmly committed to new, more ecological and sustainable materials to manufacture our cards, such as corn starch and sugar cane (PLA), plastic recovered from beaches or extracted directly from the water (Ocean Plastic) or recycled plastic (rPVC). Our commitment is to be virgin plastic free by 2030. And since we like challenges, we are ready to accept any one you can throw at us to create a truly unique card; metal, wood, carbon fibre, biometrics, aviation aluminium ... you name it!
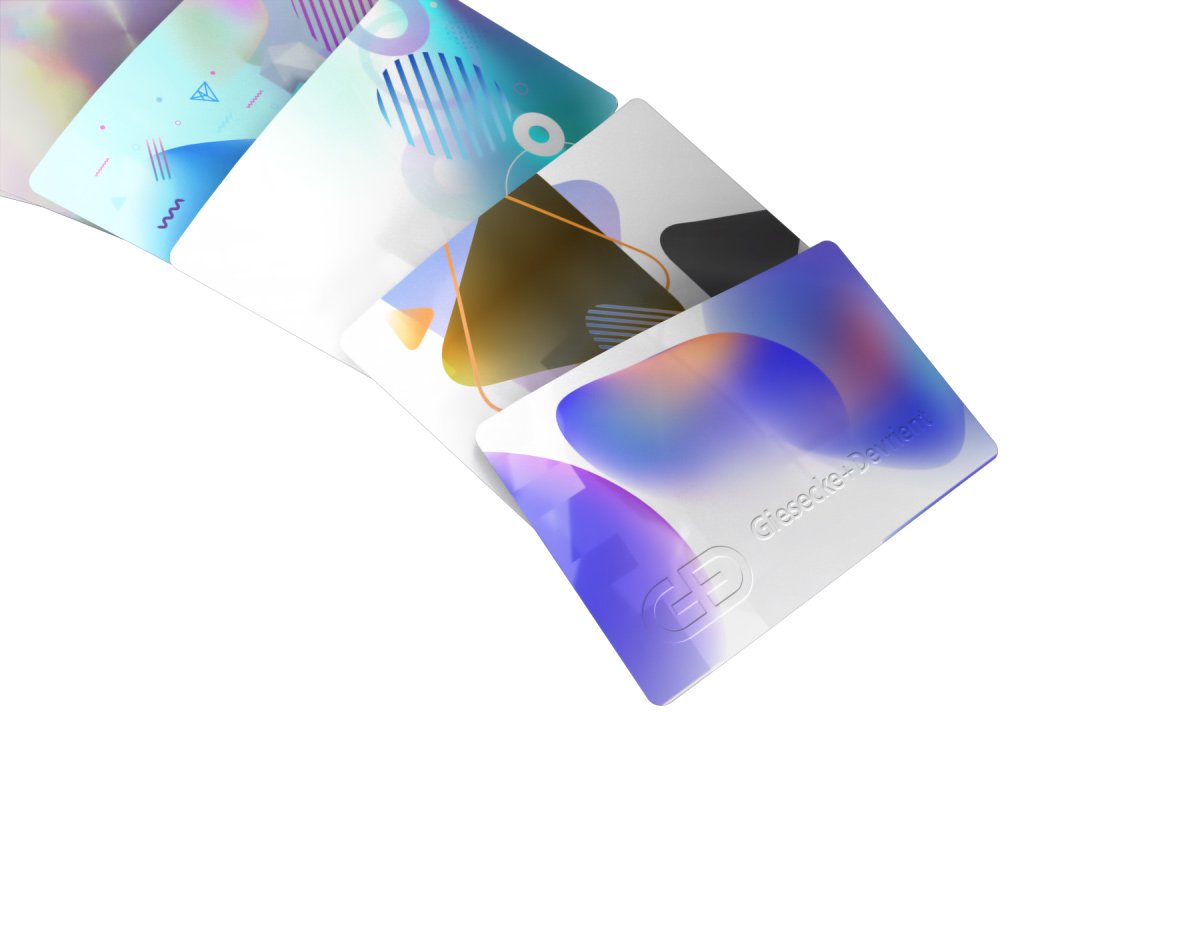
Increasing altitude
From simple white screen printing to pearlescent, metallic or translucent effects, magic inks, embossed varnishes and 3D effects...
The sky is the limit
Time for a sandwich
Once we have the printed sheets with the design on the front and back, the colours are checked with a spectrophotometer. We then move on to the collation phase in which we create the “sandwich” with the following ingredients: Overlay or protective layer on the front. Printed layer with the design on the front. Antenna inlay for Dual Interface cards. Printed layer with the design on the back. Overlay or protective layer on the back. This last layer carries the magnetic stripes which were transferred onto it in a previous step.
The sandwiches are then placed in the cassettes. Pressure and heat weld the layers together to form a single compact sheet.
Video: Printing Stage
STAGE 3 FINISHING AND IMPLANTING THE CHIP
Prepare for landing
Safety belts fastened and trays folded, we enter the final stage of the journey.
The sheets are checked and then taken to the punching unit. The punching machine rejects the cards marked as defective in the manual inspection.
The cut cards are not quite finished yet: the security features have to be added. This leads to the hot stamping process in which the payment scheme hologram and signature panel are applied. Both elements, which come in rolls, are attached on the card with pressure and heat. The process ends with a further check to ensure they have been applied correctly so we can safely continue to enjoy our trip.
Final details
MillingAt this stage of the journey we need to make the cavity to insert our security chip. A high-precision milling machine takes care of this process at cruising speed. |
|
Contact preparationConductive paste is applied over the exposed antenna wires. This will allow the chip to be connected to the antenna. |
|
Chip preparationThis is followed by the chip initialisation process in which the operating system is loaded. The chips are then coated. They are rolled through the laminator and glue is applied to them to later attach the chip to the card. |
|
Implanting the chipThe cards enter the chip implanter and mechanical arms place them in the cavity. With pressure and heat, the chip is bonded to the plastic with the adhesive placed on the reverse in the previous stage. Then, if necessary, the data required by the customer will be loaded onto the card. |
Anything to declare?
Since our travelling friend will be on the market for several years, it needs to pass a set of normative quality controls: climatic chambers, sun ageing, chemicals and a whole series of electrical tests, ATM simulations, etc.
Video: Finishing and Chip Implanting Stage
Landing. Fingers in position
Our traveler has arrived at its destination. Our company aims to ensure a smooth and turbulence-free journey with the amount of technological resources and exhaustive checks we apply to guarantee the security, reliability and quality of our cards.
We hope you have a good flight and look forward to seeing you on board again!
Get in touch
If you have any questions about our end-to-end business solutions or about our company, seek expert advice, or want to give us your feedback, our team is here to support you, anytime.